在过去十年内,端铣出现了多种进展,包括新的刀具结构设计、韧性好且耐磨的硬质合金材质、可减少机床和刀具振动并缩短加工时间50%以上并延长刀具寿命的刀具路径。这种去除金属的新方法甚至可用于轻载机床上加工诸如钛和耐热合金类难加工材料。只要掌握好加工的基本原则并用CAM系统生成必要的刀具路径,任何人都可以采用此方法进行铣削加工。
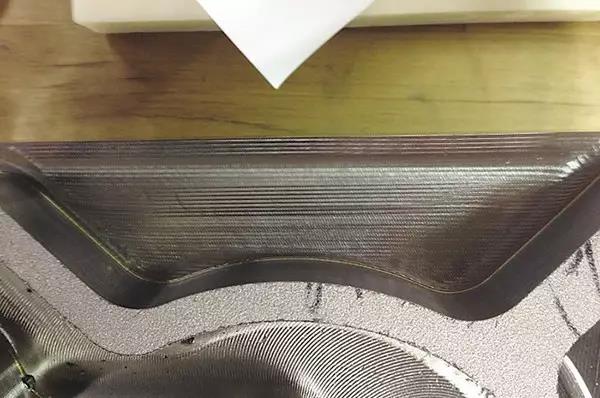
直线刀具路径铣削在工件边缘处去除材料
在采用最大性能铣削(maxi-mum-performance milling,MPM)方法之前,制造车间采用传统的铣削方法,即采用中低的进给和切削速度用于重切加工。通常,切削宽度达到刀具直径的80%以上,切削深度达到刀具直径的100%以上。
尽管采用传统方法的每次走刀可切除大量材料,但经常会导致刀具刃口微崩刃,并产生不可预期的结果和缩短刀具寿命。另外,此方法会产生大量切削热,需要采用特殊的刀具涂层来应对。对立铣刀来说,需要合理设计刀具的径向前角和芯部直径来实现重切。如果采用特殊波纹刃口设计的粗加工立铣刀或玉米铣刀,则可用来断屑并减轻重切时的刀具变形。
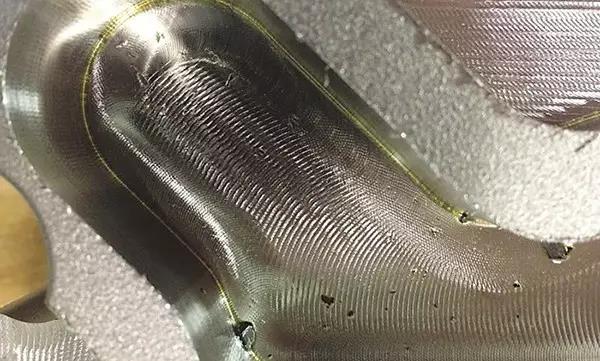
摆线刀具路径铣削适用于紧凑空间加工,如开槽和小型型腔铣削
随着数控加工中心的出现和机床刚性的提升,顺铣得以实现。顺铣加工可增长刀具寿命和提高表面质量,但也会产生振动,振动通常在径向切深为刀具直径的60%-90%时发生。一旦产生振动,前刀面将拍击工件材料,而不是卷屑和断屑。顺铣对铣刀和机床的要求都很高。
为了应对以上加工情况,机床制造商开发了功率和扭矩刚性足够的机床,在连续重载时可进行长时间加工。同时改进机床主轴,使其可承受持续载荷。刀柄夹持刀具要可靠,以消除因切削力过高而造成的掉刀现象。由于传统加工方法不属于高速加工,对刀柄的跳动公差要求不高。
最大性能铣削
航空产品供应商可能最先认识到高效加工工艺的必要性。通过优化加工机翼和其它大型平面的余量去除工艺以及降低功率消耗可实现巨大的能源节约。通过优化刀具径向路径,使每次走刀能快速进给并切除少量材料。在切削过程中,保持稳定的切削载荷以防止刀具振动和损坏。
高效加工的方法之一是直线刀具路径铣削,即采用径向小切深和轴向大切深的刀具,沿工件内部或外部直线运动。顺铣时切屑由厚 到薄变化且径向切削轻快,因此可采用大进给和切削速度的方法来实现最大性能铣削,这种加工方法可减少切削热和降低切削力。
型腔中心显示螺旋坡铣的终止位置以及螺线铣的开始位置,当铣刀进入较窄的区域时开始摆线铣削
另一种高效加工方法是摆线刀具路径铣削,一种包含向前移动和逐步进刀的圆形铣削方式。铣刀沿螺线移动,重复层切被加工材料。摆线是一种2D刀具轨迹,也可用来铣槽和开腔,以解决空间狭小处的排屑问题。另外,摆线铣削也可用来清除零件型腔内部粗加工铣削时留下的大圆角。
曲线螺线也称为渐变螺线,通常用于型腔铣削2D刀具路径。通过等步距进刀直到加工完成零件特征,可减少不必要的刀具加速和减速。对所有的最大性能铣削方法,采用密齿立铣刀可增加进给速度,带来更高的金属去除率。
最大性能铣削的另一种类型用于型腔铣削。型腔铣削通常需要先加工出一个起始孔,可采用钻头钻削或用底齿过中心的立铣刀进行螺旋坡铣加工出起始孔。螺旋坡铣时,立铣刀除沿直径可达自身直径2倍的圆周旋转运动外,还同时沿Z轴向下进刀直到轴向深度。刀具沿圆周可顺时针或逆时针运动,从而产生顺铣或逆铣。
所有的最大性能铣削方法可能会用于同一零件的加工,这主要取决于零件的几何特征、排屑以及现有CAM系统,并确定最适合的加工方法。
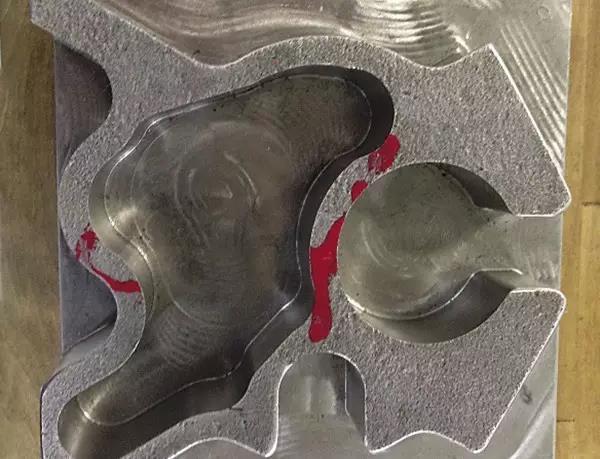
此测试件采用本文中所有的刀具路径方法
大芯轴直径立铣刀适用于最大性能铣削,可提高刚性和保证高速进给。刀具铣削时的包角和切深需尽可能保持恒定,严格禁止在零件拐角处包角过大导致埋刀加工。
加工的先决条件
最大性能铣削可有效应用于多种材料的加工。为了正确使用这种加工方法,需要一些先决条件,比如一个优秀的CAM系统。生产周期的缩短是评价CAM系统的主要指标,另外,系统的易用性和缩短编程时间也是重要的考量指标。在自有设备上加工出正确的测试件可确保检查CAM系统的工作效能。
相对于传统铣削,最大性能铣削的进给速度可提高10倍以上。机床的控制或伺服系统必须快速和精确,以避免拐角处的过度加工或因为数据不足造成加工减速,并导致因进给不够快速引起的刀具磨蚀加工。
最大性能铣削的主轴转速较传统加工方法可提高4-5倍,这主要取决于工件材料。当主轴转速超过10000rpm,需采用动平衡良好的刀柄。尽管最大性能铣削的切削力很小,刀具掉刀仍是一个需要考虑的问题。因为最大性能铣削在更少的时间内切除更多的工件材料,推荐使用热套、液压夹头或带安全锁的刀柄,不推荐使用侧固刀柄。
一旦满足最大性能铣削的所有要素,就可以按照测试—文档编制—加工工艺制定的顺序开始工作,甚至老式机床设备也可采用最大性能铣削。